GREEN SOLUTION FOR ALL CONSTRUCTIONS
Safe for users, environmentally friendly while still ensuring excellent sound insulation, waterproofing, mold resistance, high durability and application, being compatible with many types of materials, so Remak® XPS is currently evaluated as the leading green material in the sustainable construction trend of the future, a green solution for all constructions.
Remak® XPS – A Green Solution for the Future
Remak® XPS is produced according to modern production lines and technology, as well as high quality raw materials which are green, clean, and environmentally friendly. According to scientists’ estimates, with the conversion of using CO2 instead of HCFC-22 in the production of Remak® XPS foam, each year we can reduce up to 460 million tons of CO2 emissions into the environment, contributing to completely eliminating 100 tons of HCFC-22 in the field of XPS foam production in general in Vietnam.
And of course, Remak® XPS is the most effective solution for thermal insulation in buildings. The application of XPS insulation for roofs and walls can cut energy use in half. In Europe, for example, using XPS insulation foam in buildings save roughly of 3.3 million barrels of oil per day.
In fact, recent studies of newly constructed buildings prove that: commercial buildings using XPS insulation panels with a thickness of 15-18cm can save annual electricity consumption from 343-344KWh /m2 (www.styropor.de). It is equivalent to every year, every 1m2 of XPS insulation used will save about 1,000,000 VND (electricity price 2500 VND/KW). When compared to heating oil consumption, 1kg XPS saves about 400 liters of heating oil over 50 years.
Moreover, Remak® XPS is made from virgin Polystyrene plastic, so it can be recycled while still ensuring its superior performance and properties, helping to reduce waste and environmental pollution.
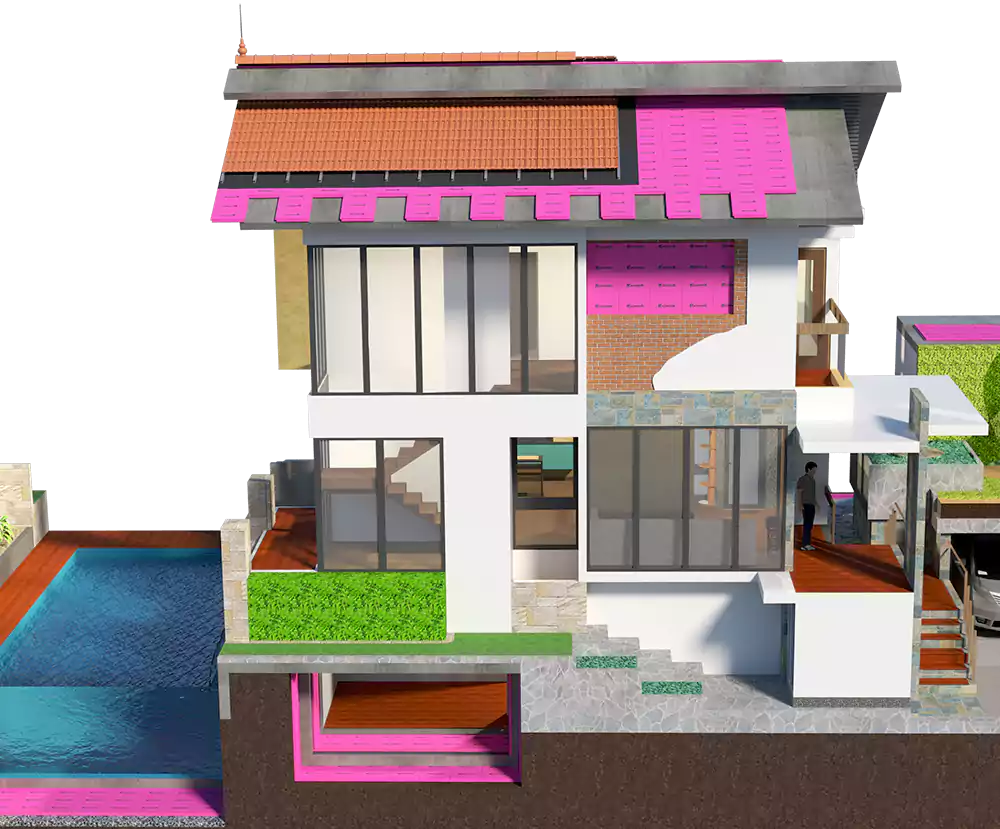
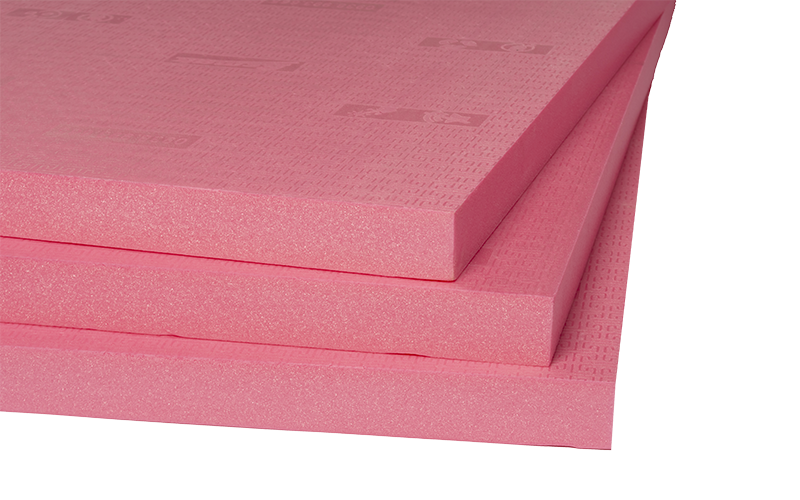
Notably, on the market, XPS foam is currently produced with 2 popular types: the sufficient density is from 32-35kg/m3 and the high density type is from 38-40kg/m3. Meanwhile, low density XPS (from 24-32kg/m3) currently very few manufacturers can produce. The reason is that the production process of low density XPS is complicated, many times more difficult than that of full and high density XPS, requiring modern technology & machinery and a skilled production team.
Among the Top 4 XPS manufacturers on the Vietnamese market today, Remak is one of the first units to successfully research and manufacture Remak® XPS low-density and recycled Remak® XPS products for savings market segmentation. This is a strategy to bring optimal value and benefits to customers, with a focus on those with limited budget but still need to construct sound insulation, heat insulation, waterproofing and moisture resistance, ensuring comfortable living and working condition.
So far, large-scale projects with high soundproof and heat insulation requirements/standards such as apartments, buildings, commercial buildings, and factory buildings… often use mineral wool, glass wool (much higher cost than Remak® XPS foam). Meanwhile, residential buildings with extremly tight budgets still can use low-density Remak® XPS and recycled Remak® XPS to renovate the space, providing a more comfort, convenience and safety place to live, work, and rest.